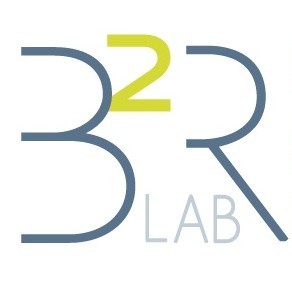
Location: Università degli Studi di Napoli Federico II – “Scuola Politecnica e delle Scienze di Base”
Lab head: Prof.ssa Fanny Ficuciello
Contact: fanny.ficuciello@unina.it
Lab Team
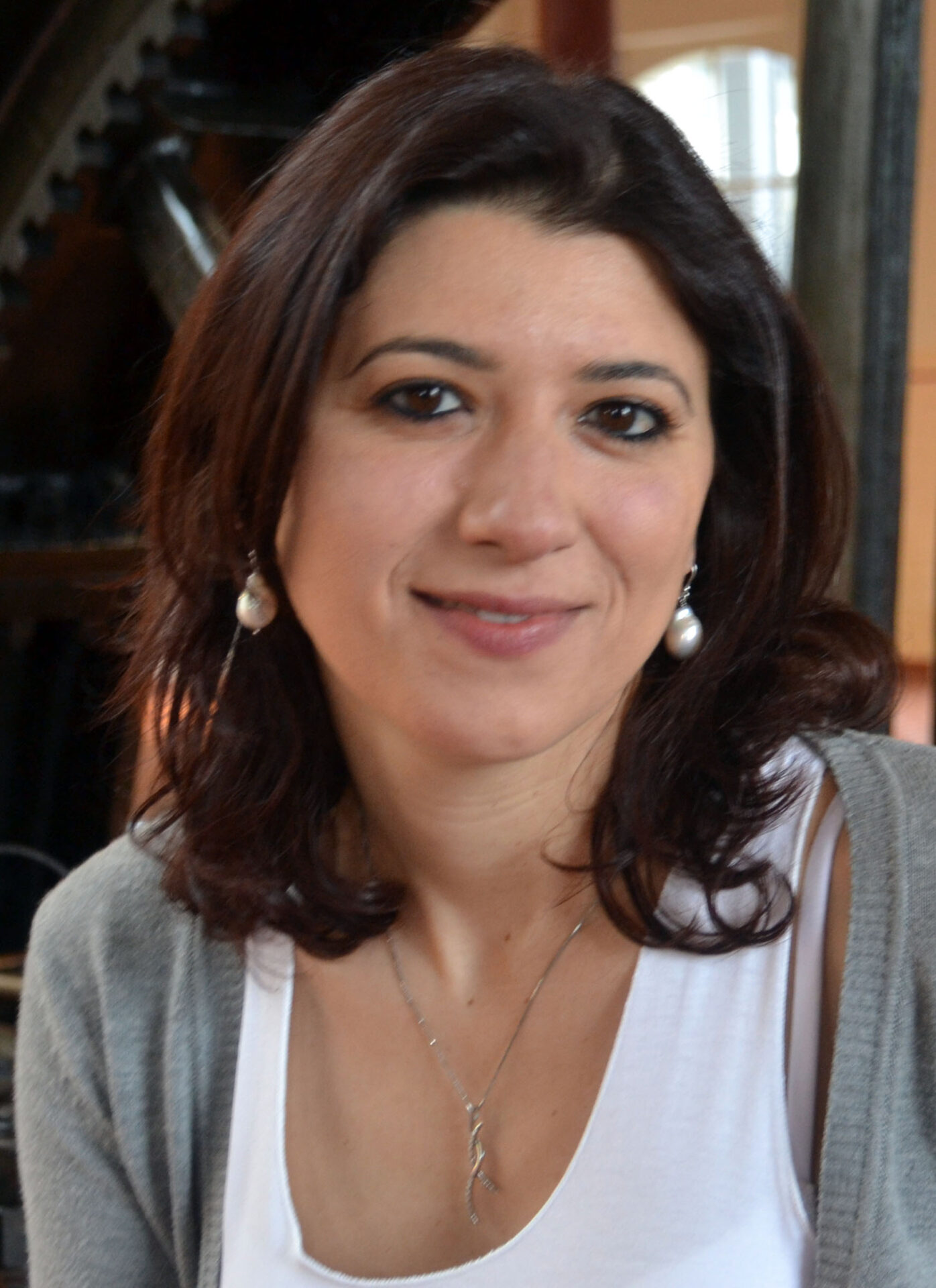
Fanny Ficuciello
Associate Professor
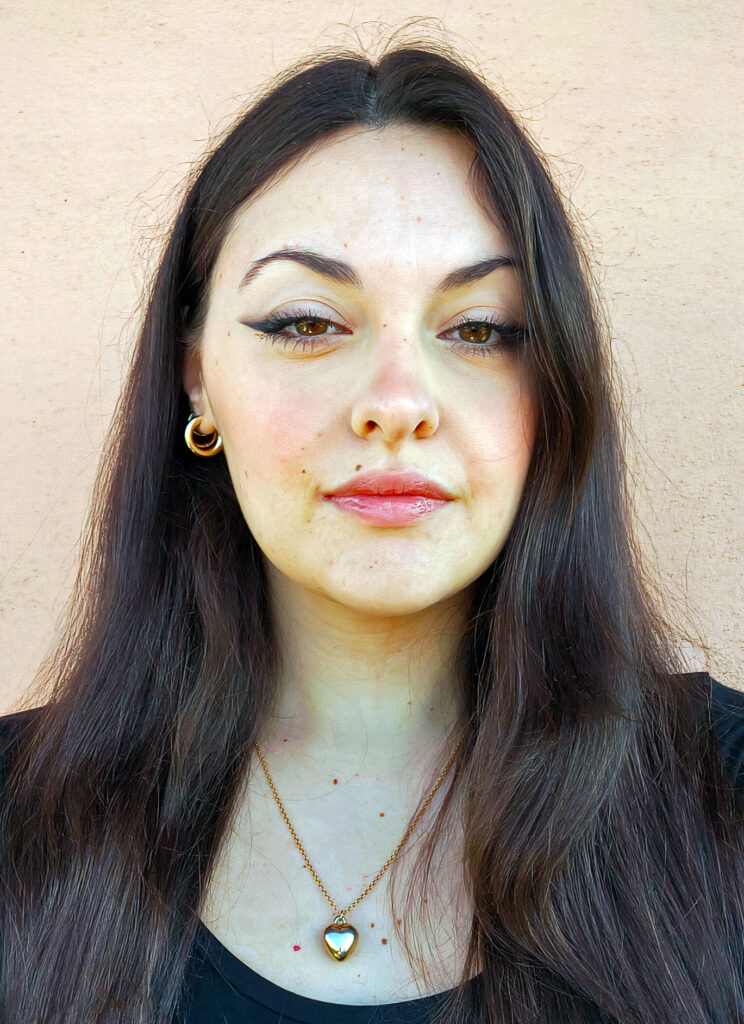
Antonella Imperato
Ph.D Student
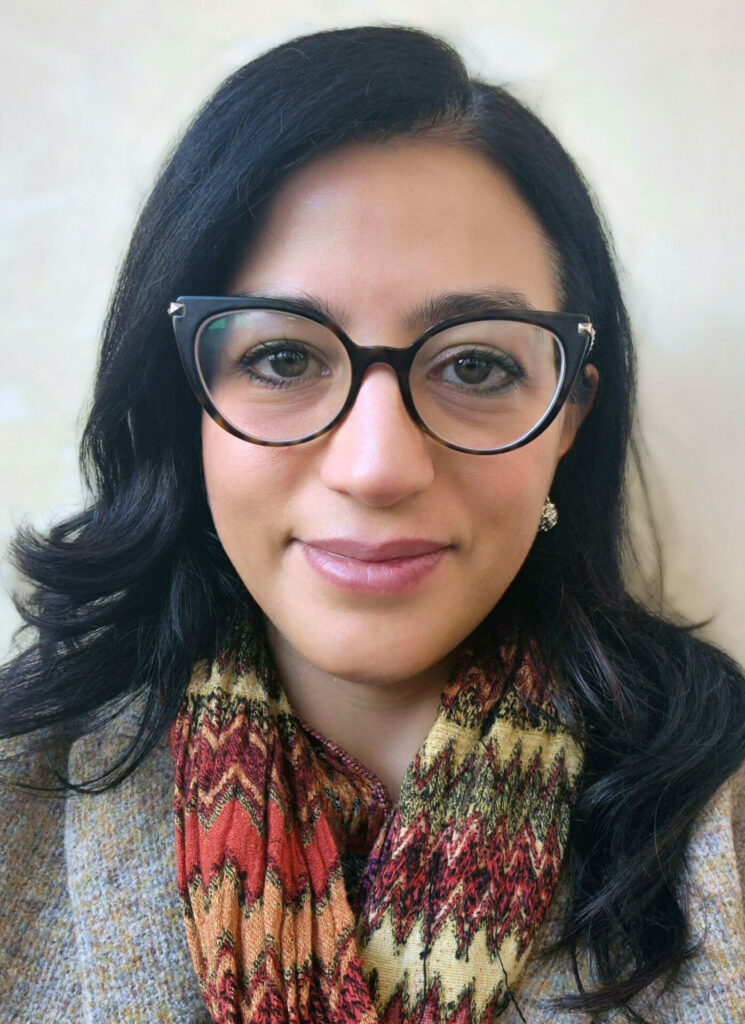
Sara Ebraico
Administrative Assistant
Francesco Schetter
Research Assistant
Lab Mission
B2R Lab (Biomimetic and Biohybrid Robotics Laboratory) is the new facility of the PRISMA Team for the design and fabrication of soft and bioinspired robots aimed at medical applications, prostheses and exoskeletons as well as their biological interfaces to communicate with the human body. The lab is equipped with lower/upper limb prostheses and exoskeletons, both commercial robots and internally developed prototypes. The Lab has optical tracking systems, emg sensors, treadmills, and in general rehabilitation systems, 3D printers in silicone and polymeric material, as well as tools for rapid prototyping of soft robots.
Devices
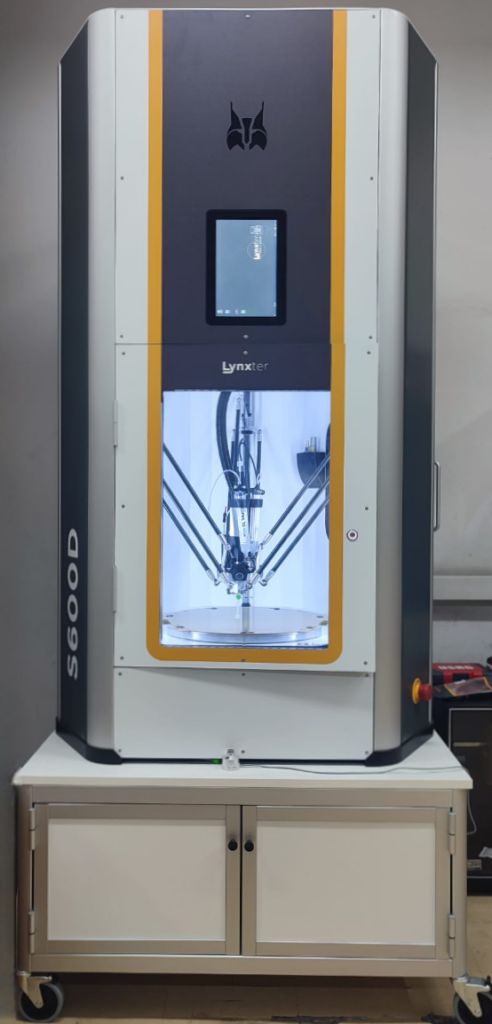
Lynxter 600D
The system is a one-of-a-kind 3D printer designed for maximum versatility and performance. Thanks to its quick-change toolhead technology, it seamlessly switches between different printing processes, supporting a wide range of high-quality materials, including thermoplastic filaments and liquid silicones. Its open technology ensures adaptability and customizability for advanced users, while high-temperature printing capabilities and large build volumes make it suitable for both prototyping and industrial-scale production.
Data sheet: download
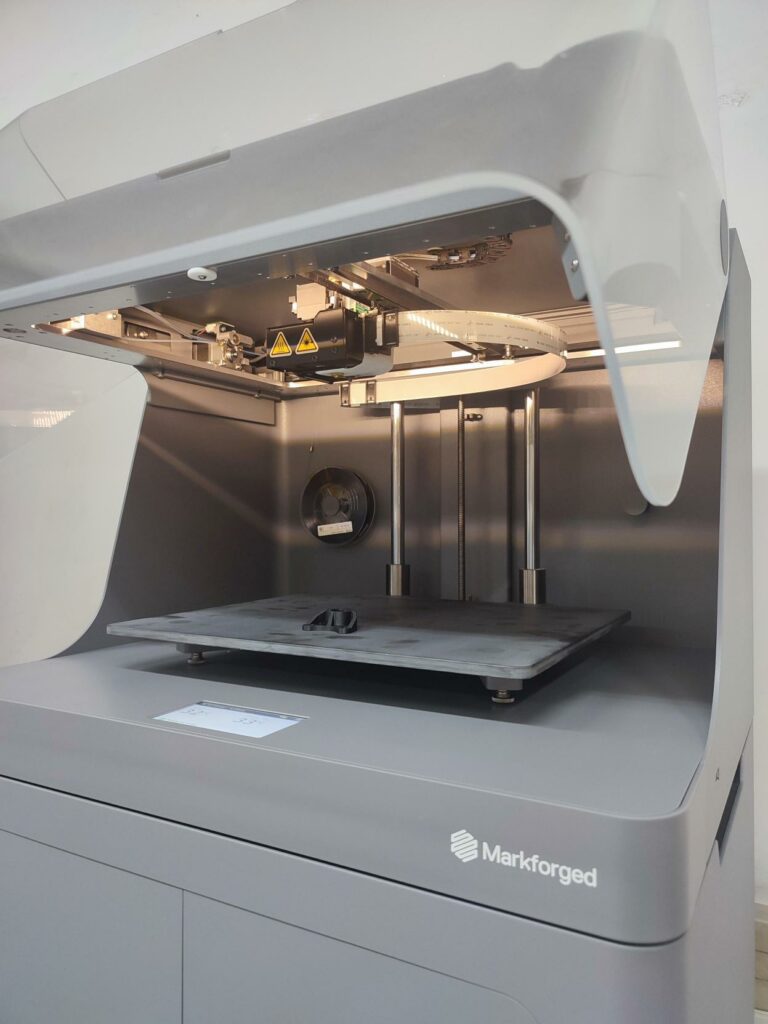
Markforged X7 Printer
This solution enables 3D printing with carbon fiber reinforced components, delivering exceptional strength and durability. It integrates laser scanning with micron-level precision for advanced calibration, ensuring consistently high-quality results. The system also includes dimensional accuracy verification powered by Blacksmith adaptive manufacturing technology, which autonomously adjusts and corrects deviations in real time. Additionally, Turbo Print mode, the fastest printing mode developed by Markforged, significantly accelerates part production without compromising precision.
Data sheet: download
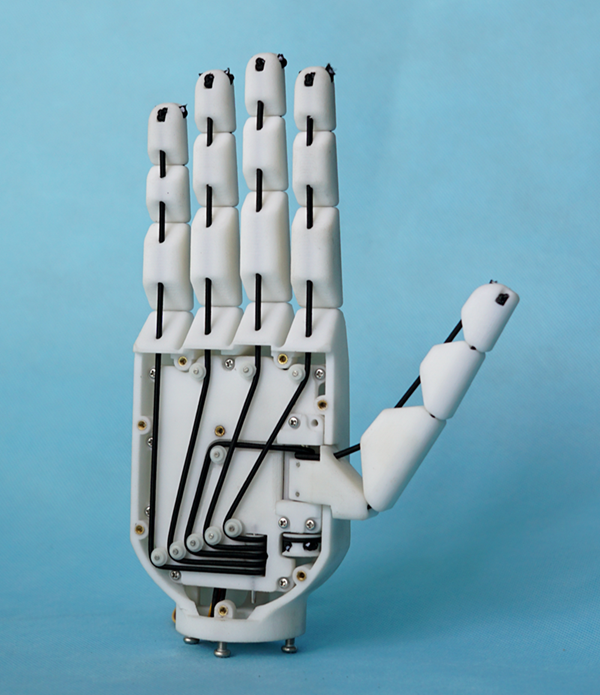
MERO Hand
This 3D-printed robotic hand is a lightweight and versatile prototype featuring 16 degrees of mobility, allowing for realistic emulation of human hand movements. It uses tendon-driven actuation, powered by 2 motors that effectively control the main joints. At its core, the hand is operated by an Arduino UNO microcontroller, which coordinates finger motion and responsiveness. Weighing just 336 grams (excluding the controller), it is well-suited for educational, research, and prototyping purposes in the field of robotics.
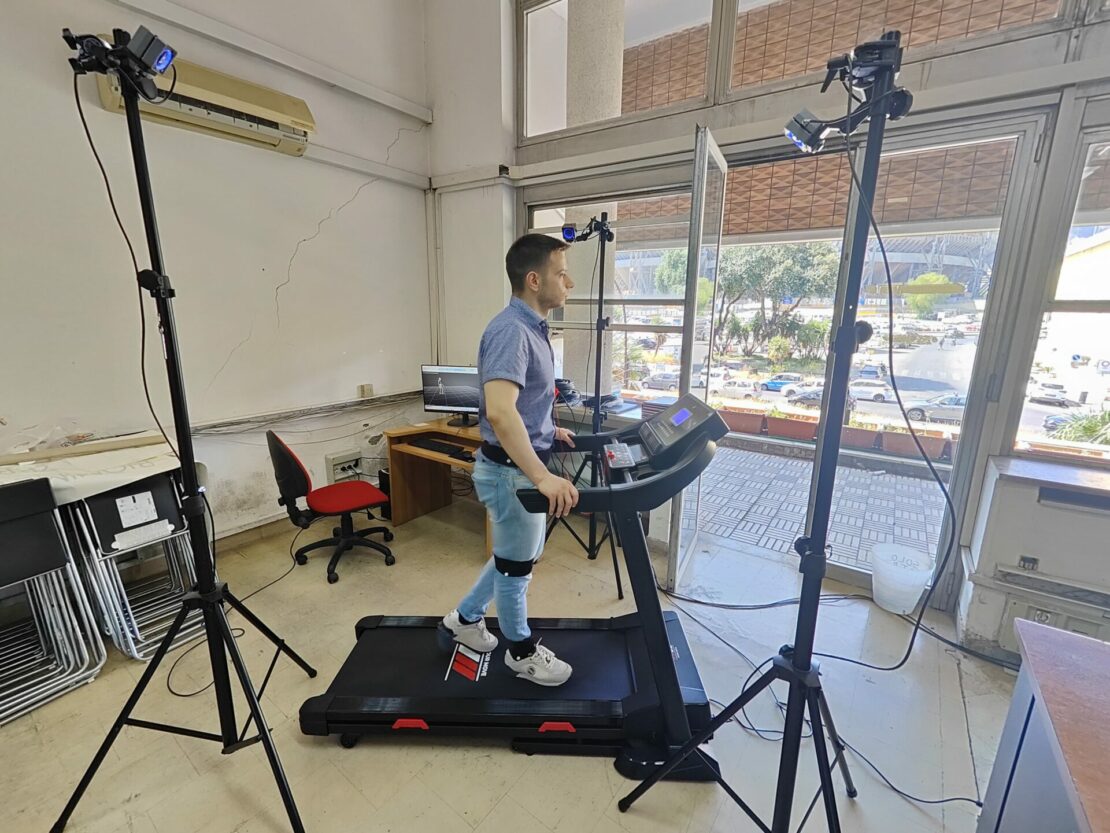
Optitrack Motion Capture
The system features 6 high-speed cameras optimized for precise tracking of bodies and objects across 6 degrees of freedom (DoFs), ensuring accurate spatial positioning and orientation. It supports real-time motion streaming to third-party software using proprietary or standard protocols such as VRPN and TrackD, allowing for seamless integration. Furthermore, it can be combined with various systems, such as EMG sensors, making it an ideal solution for applications in biomechanics, robotics, and virtual reality.
Data sheet: download
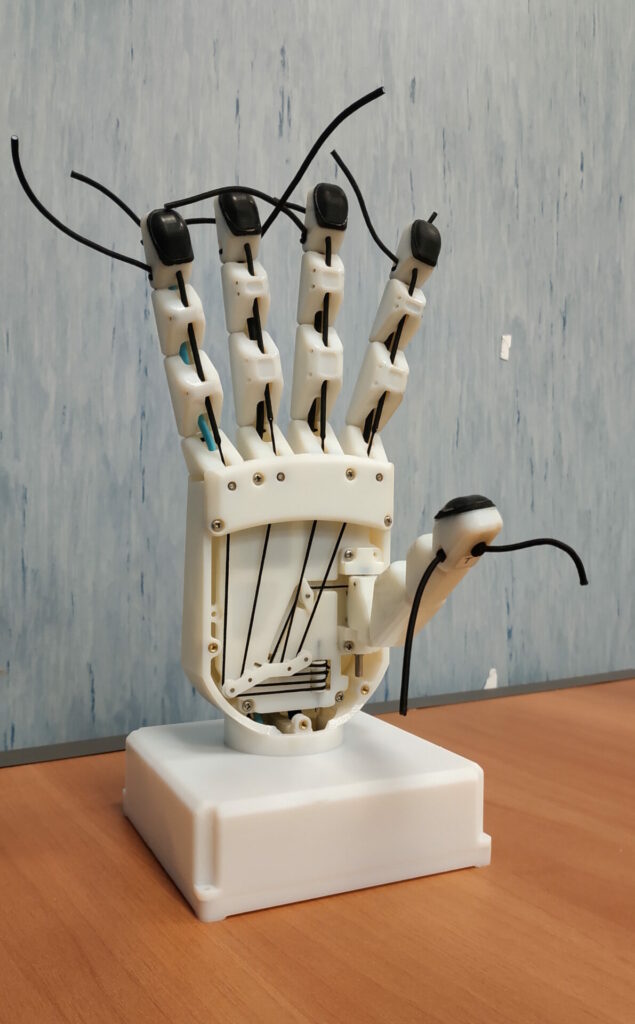
PRISMA Hand II
This 3D-printed robotic hand is designed with 18 degrees of mobility, achieved through tendon-driven actuation powered by 3 motors. It features motor position sensors for precise motion control and tactile sensors at the fingertips to enhance interaction with the environment. Controlled by an Arduino UNO microcontroller, the hand weighs 336 g (excluding the controller). The integration of advanced mechanics and sensing capabilities makes it an excellent solution for humanoid robotics, prosthetics, and research applications.
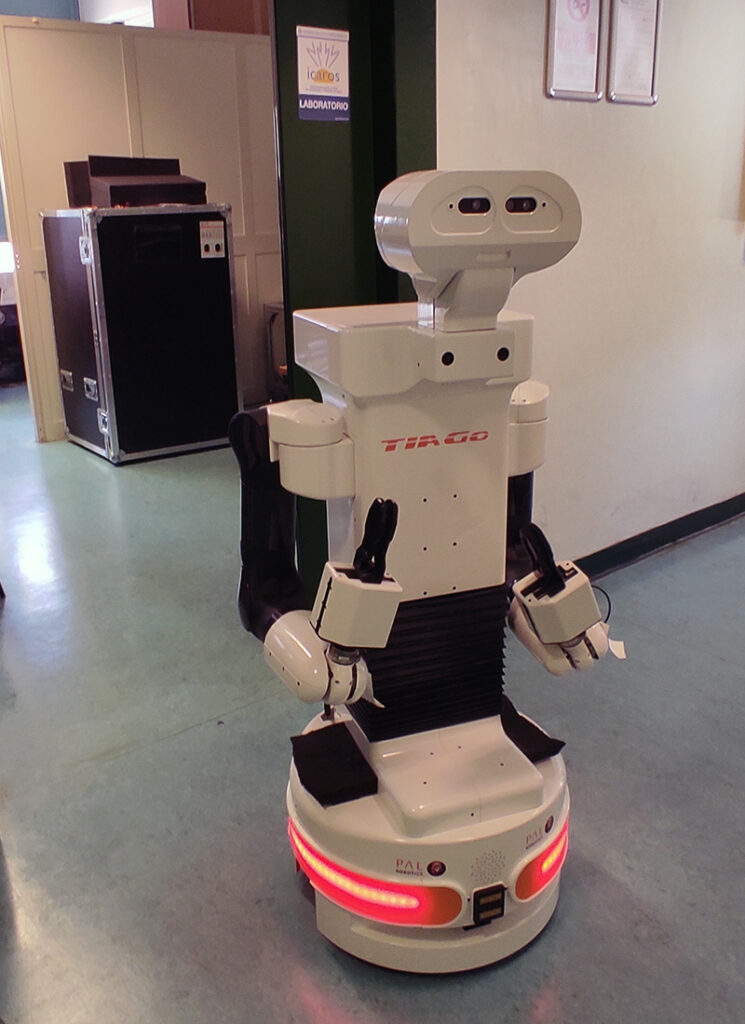
TIAGO++
This is a bimanual mobile robotic platform designed for dynamic environments and advanced human-robot interaction. It features a differential-drive mobile base with a maximum speed of 1 m/s, along with two 7-degree-of-freedom arms, a 1-DoF torso lift, and a 2-DoF head, enabling versatile manipulation capabilities.
The sensing suite includes an RGB-D camera, 6-DoF IMU, a 10-meter laser, and three 1-meter sonar sensors, providing comprehensive spatial awareness. The audio system comprises two 5W speakers and a 2-microphone array with stereo output.
Powered by an Intel i7 CPU, with 16 GB RAM and a 500 GB SSD, it runs on two 36V 20 Ah batteries. Connectivity is provided via 802.11 n/ac Dual Band Wi-Fi and Bluetooth 4.0.
The robot is capable of autonomous navigation, SLAM, manipulation, perception, speech recognition, and human-robot interaction, making it a complete solution for research and service robotics.
Data sheet: download